Profili di Rischio di Comparto Asfaltatori Stradali
PROFILI DI RISCHIO DI COMPARTO ASFALTATORI
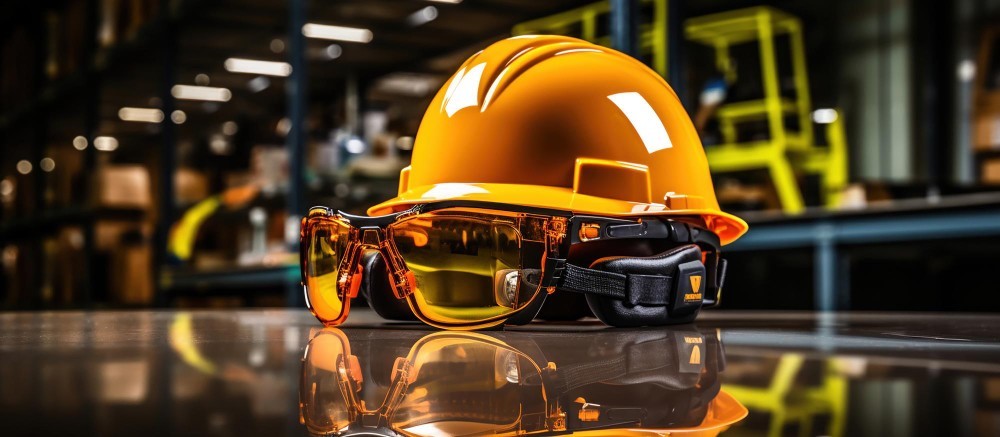
PREFAZIONE AL COMPARTO
Tra i lavoratori del settore edile gli addetti alle opere di asfaltatura appaiono costituire un sottogruppo con caratteristiche lavorative e di rischio del tutto peculiari, solo recentemente giunte all’attenzione della ricerca nazionale ed internazionale. Una valutazione integrata che focalizzi l’attenzione sulle principali criticità e traduca in termini applicativi le più recenti nozioni scientifiche, fornendo opportune indicazioni di prevenzione efficaci ed efficienti nonché di pratico utilizzo, è parsa un utile ed agevole strumento di lavoro per la realtà nazionale.
Particolare attenzione è stata rivolta verso le sostanze chimiche (infortuni, effetti tossici, incendio/esplosione), l’utilizzo di macchine (infortuni, rumore, scuotimenti, vibrazioni,
videoterminale), l’ambiente di lavoro (infortuni, microclima, polveri, agenti biologici,
radiazione solare ultravioletta), la movimentazione di carichi (con macchine, manuale), l’organizzazione del lavoro e gestione delle emergenze.
Attenzione è stata rivolta anche alle interazioni con il contesto circostante lo svolgimento delle lavorazioni specifiche (edifici ed altri cantieri, circolazione e
viabilità, inquinamento atmosferico e acustico, sicurezza dei pedoni e segnaletica).
INDIVIDUAZIONE E DESCRIZIONE GENERALE DEL COMPARTO
Con il termine “comparto asfaltatori” si è inteso raggruppare l’insieme delle aziende dedite alla produzione di asfalto, all’asfaltatura di strade ed all’asfaltatura di marciapiedi.
Questo tipo di attività viene generalmente ricompreso tra le attività edili, ma nella realtà è caratterizzata da precise peculiarità che la rendono meritevole di attenzioni particolari ed analisi dei rischi dedicata sia per gli aspetti di salute sia per quelli di sicurezza.
Necessaria premessa per potere comprendere a pieno i rischi connessi con il comparto asfaltatori, è prestare la giusta attenzione al significato di alcuni termini fondamentali. In particolare per “asfalto” o “conglomerato bituminoso” (“asphalt mix” negli Stati Uniti d’America), si intende una miscela (naturale o artificiale) di bitume ed elementi litici di varia granulometria (materiale inorganico inerte). Il “bitume” (negli Stati Uniti definito “asphalt”), è invece un materiale legante naturalmente presente in natura e ottenuto in raffineria dalla lavorazione del petrolio greggio. Esso contiene composti organici di origine prevalentemente idrocarburica, con tracce di zolfo, azoto, ossigeno, nichel, ferro e vanadio. In particolare tra i composti organici ad alto peso molecolare sono prevalenti gli idrocarburi con un numero di atomi di carbonio maggiore di 25 e con un alto valore del rapporto C/H, tra cui gli idrocarburi policiclici aromatici. Si tratta di un materiale di colore bruno o nerastro, con comportamento termoplastico, solido o
semisolido, non volatile a temperatura ambiente, non solubile in acqua. In commercio si
trova oltre che in forma semisolida (che è quella più adoperata), anche sottoforma di bitume liquido o emulsione bituminosa. Lo stato di bitume liquido o di emulsione è provvisorio, desiderato per esigenze applicative ed ottenuto lavorando il bitume con acqua alcalinizzata, additivi e solventi. Con il termine “catrame”, corrispondente all’inglese “tar”, ci si riferisce invece ad un materiale viscoso che seppur dotato di aspetto simile al bitume, se ne differenzia per origine e composizione chimica. Esso, infatti, è ottenuto tramite un processo industriale di distillazione distruttiva del carbon fossile e rispetto al bitume mostra un contenuto nettamente più elevato di idrocarburi policiclici aromatici (IPA), oltre che numerosi altri composti contenenti ossigeno, azoto e zolfo. In passato, nei paesi sprovvisti di asfalto naturale, come ad esempio l’Inghilterra, il catrame era diffusamente impiegato per la pavimentazione stradale (tarmacadam), a volte anche in miscela con il bitume. Tale uso, ora del tutto cessato e praticamente sconosciuto in Italia, ha favorito l’attuale confusione esistente ancora tra i termini catrame e bitume nel linguaggio comune ed in molti ambiti professionali. Generalmente le attività di asfaltatura sono svolte da aziende di piccole (da poche unità ad una decina di operai) o medie dimensioni (30-100 operai). In quest’ultimo caso, tuttavia, le attività svolte dall’impresa non sono limitate alla sola produzione dell’asfalto e pavimentazione ma coprono altri settori dell’edilizia civile: principalmente demolizioni, scavi e movimento terra, opere idrauliche, costruzioni civili (opere di urbanizzazione primaria e secondaria). Volendo restringere il conteggio ai soli dipendenti addetti alla specifica attività di asfaltatura, questo è compreso in un intervallo più stretto (3 e 35).
Gli addetti alle opere di asfaltatura sono generalmente lavoratori dipendenti, il cui rapporto di lavoro è regolato dal contratto collettivo nazionale dell’edilizia. In particolare si tratta di operai edili specializzati, affiancati da uno o due operai semplici cui sono affidati i compiti che richiedono le competenze minori (trasporto carriola, utilizzo badile, sbandieratore), che lavorano in squadre di 3-10 persone.
Il carico di lavoro varia nell’arco dell’anno con picchi di attività, che si registrano nei periodi primavera-estate. La dipendenza dalle condizioni meteorologiche comporta un frequente ricorso a periodi di forzata inattività o re-impiego in attività differenti.
IL CICLO LAVORATIVO
Prima di addentrarsi in una disamina del ciclo tecnologico occorre fare un cenno all’entità intorno a cui ruotano le opere di asfaltatura: la strada. Essa ha una struttura architettonica complessa definita da precise caratteristiche tecniche, costruttive e funzionali. Schematicamente risulta essere costituita da tre strati:
- strato di usura a diretto contatto con le ruote dei veicoli;
- strato di collegamento tra lo strato di usura e la fondazione (base);
- fondazione.
L’insieme di questi strati nelle pavimentazioni in conglomerato bituminoso è chiamato “manto”. In particolare gli strati più superficiali sono realizzati con conglomerati bituminosi, mentre le fondazioni possono essere realizzate se rigide con calcestruzzo di cemento, se flessibili con una massicciata di pietrame o con ghiaia cilindrata o con un manto di terra stabilizzata oppure con strati di scorie, macerie, misti di cava, ecc.
Si definisce sottofondo il terreno sul quale è poggiata la soprastruttura e il più direttamente interessato dall’azione dei carichi esterni. Esso può essere formato da terreno di scavo o di riporto, spesso trattato allo scopo di ottenere un aumento della capacità portante ed una riduzione della sensibilità all’azione dell’acqua e del gelo. La superficie che delimita superiormente il terreno di sottofondo costituisce il piano di posa della sovrastruttura.
Le operazioni di asfaltatura possono essere distinte in tre lavorazioni principali:
1) Produzione conglomerato bituminoso;
2) Asfaltatura strade;
3) Asfaltature marciapiedi.
ATTIVITÀ DI PRODUZIONE CONGLOMERATO BITUMINOSO
Per produrre il conglomerato bituminoso si deve procedere alla miscelazione a caldo di bitume e inerti in opportune proporzioni. Più dettagliatamente la ricetta dell’asfalto prevede quantità percentuali in peso di aggregati lapidei pari al 90%, di filler al 3-10%, di bitume al 4-7%, di additivi allo 0-2%.
I materiali litici vengono adoperati sotto forma di elementi frantumati di varie dimensioni, in modo da ottenere un ammasso granulare di elevata densità, ove i vuoti che rimangono tra gli elementi più grossi vengono riempiti da elementi più piccoli. Mediante l’utilizzo di crivelli e setacci, vengono distinti i vari assortimenti granulometrici (ciottolo, ghiaia, ghiaietto, ghiaino, sabbia).
Il filler è il materiale polverulento con granulometria più bassa, inferiore a 0,075 mm; esso all’interno degli asfalti svolge la duplice funzione di completamento del fuso granulometrico (con aumento della stabilità), e di stabilizzazione del legante bituminoso (con riduzione della suscettibilità termica).
Gli additivi sono prodotti naturali o artificiali che, se aggiunti alla ricetta consentono di migliorare le prestazioni dei conglomerati bituminosi, modificandone le caratteristiche fisiche e meccaniche. In particolare gli additivi di più comune utilizzo sono polimeri, attivanti di adesione, additivi flussanti, pigmenti.
Variando la granulometria e la natura degli aggregati litici, il contenuto di bitume e aggiungendo additivi è possibile ottenere svariati tipi di conglomerati bituminosi destinati ad impieghi quanto mai vari.
2.1 – DESCRIZIONE DELLA FASE DI LAVORAZIONE
La prima fase di lavorazione è costituita dall’approvvigionamento e stoccaggio delle materie prime.
Gli aggregati lapidei a differente granulometria possono essere acquistati direttamente da cave che estraggono minerali calcarei, oppure sono costituiti dal frantumato di materiale di recupero ottenuto mediante operazioni di fresatura stradale o di scavo. Per
il trasporto in azienda degli inerti vengono adoperati camion a cassone ribaltabile
che consentono anche un agevole scarico del materiale nelle apposite aree di toccaggio. In particolare le scorte degli inerti sono distribuite su di un piazzale, in cumuli separati secondo le varie pezzature
Il filler di nuova produzione giunge in azienda trasportato all’interno di autocisterne, dalle quali viene scaricato tramite conduttura e stoccato all’interno di silos dedicati
Il bitume è acquistato dalle raffinerie che provvedono anche al trasporto mediante autobotti in azienda, dove viene stoccato in serbatoi metallici coibentati e dotati di riscaldamento a circolazione di olio
Il tipico impianto di produzione di asfalto per strade può essere schematizzato nei seguenti componenti:
- Impianto di predosatura ponderale;
- Impianto di pretrattamento o essiccazione;
- Torre di mescolazione;
- Silos di stoccaggio del conglomerato.
L’impianto di predosatura ponderale è costituito da una serie di tramogge, destinate ciascuna ad un diverso aggregato litico (Figura 2-5); nella parte inferiore di ciascuna tramoggia è posto un sistema dosatore che consente il prelievo automatico della quantità desiderata di materiale (Figura 2-6). Con l’ausilio di pale meccaniche l’aggregato viene prelevato dai cumuli presenti nelle aree di stoccaggio e caricato nella serie di tramogge (Figura 2-7). Il sistema dosatore pesa e seleziona le quantità desiderate di inerti che, passati per caduta attraverso una porta di scarico, pervengono all’impianto di
pretrattamento o essiccatore mediante un nastro trasportatore
L’essiccatore (impianto di pretrattamento) è un forno a tamburo ruotante in acciaio leggermente inclinato nel senso di avanzamento del materiale. Esso è munito all’interno di alette sporgenti, che sono sagomate in modo tale da permettere l’avanzamento dell’aggregato e da effettuare un suo movimento di sollevamento-caduta attraverso la corrente di gas caldi. Il riscaldamento a temperature di 150-160 °C consente la perfetta asciugatura degli elementi litici che si possono così legare in modo più saldo al bitume. Sui fumi prodotti dall’essiccatore uno sgrossatore opera un abbattimento delle particelle con diametro compreso tra 0,075 mm e 2 mm, che vengono recuperate e utilizzate come sabbia. I filtri a manica, tramite lunghi tubi di tela consentono un ulteriore abbattimento con recupero di particelle con diametro inferiore a 0,075 mm, poi utilizzate come filler. Gli aggregati, una volta essiccati, devono essere nuovamente vagliati, allo scopo di assicurare il raggiungimento delle granulometrie finali, e pesati, per ottenere un esatto rapporto di miscela. Essi quindi, man mano che fuoriescono dall’essiccatore, giungono alla torre di miscelazione (tramite un elevatore a tazze o altro idoneo dispositivo), dove un riselezionatore li vaglia e riclassifica, quindi per caduta pervengono nelle tramoggie
del sistema di pesatura, ed infine vengono immessi nel mescolatore
Il filler, conservato all’interno di silos, viene avviato tramite coclee ad un elevatore a tazze, che lo trasporta verticalmente fin sulla torre di mescolazione, dove viene raccolto direttamente all’interno della tramoggia del sistema dosatore specifico. Le polveri fini di recupero, provenienti dai filtri dell’impianto, vengono reintrodotte nel ciclo di produzione tramite coclee. Il filler è aggiunto sempre freddo agli altri componenti.
Il bitume, riscaldato all’interno dei serbatoi tramite calore ceduto da olio circolante in serpentine, è immesso previa pesatura nella zona di mescolazione attraverso gli ugelli della barra di spruzzatura ad una temperatura di 150-160 C°. Esistono impianti con lavorazione in continuo, che sono dotati di un meccanismo automatizzato per la regolazione della portata a seconda della quantità di inerti inviata al miscelatore.
Gli inerti a granulometria voluta, il bitume, il filler ed eventuali additivi (provenienti
con ciclo chiuso da silos dedicati) confluiscono all’interno di un mescolatore in acciaio
a forma di trogolo con fondo apribile, dotato di alberi rotanti sui quali sono montati bracci e palette. I due alberi paralleli, con palette sfalsate, ruotano in senso contrario muovendosi secondo superfici parzialmente compenetranti.
Conclusa la fase di mescolamento il prodotto finito può essere scaricato dal mescolatore, posto in posizione sollevata dal suolo, direttamente sugli autocarri addetti al trasporto.
L’impianto descritto, di tipo tradizionale possiede uno specifico essiccatore per gli aggregati distinto dal mescolatore. Nelle apparecchiature tipo “Drum Mixer” (impianti di non recente concezione e piuttosto imprecisi, ma ancora utilizzati perché semplici e poco costosi), l'intero ciclo produttivo avviene invece in una sola unità rappresentata dal cilindro rotante, il quale provvede sia alla fase d'essiccazione/riscaldamento degli aggregati, sia a quella di miscelazione. I vantaggi di questi impianti rispetto ai tradizionali risiedono nel maggiore rendimento termico e nel minor numero di macchine presenti nell'impianto con ridotte necessità d'energia elettrica e di manutenzioni.
In alcune ricette è previsto l’utilizzo anche di fresato (fino al 30% in peso), che viene frantumato con mulino, possibilmente vagliato per distinguerne la granulometria e mescolato agli altri aggregati già caldi.
Gli impianti moderni possono essere gestiti da sole due persone: un addetto al controllo del processo produttivo automatico ed un addetto al carico dei predosatori con pala meccanica. Tutte le apparecchiature di comando e controllo, che concorrono al funzionamento dell’impianto, sono centralizzate in una cabina collocata in posizione strategica. Dalla sua postazione l'operatore può, per mezzo delle strumentazioni disposte su di una consolle, impostare tutte le grandezze fisiche necessarie al processo produttivo e determinare il ritmo di produzione, la quantità e qualità di prodotto e la temperatura finale degli aggregati.
L’impianto di produzione di asfalto per marciapiedi, detto anche “asfalto colato” (conglomerato contenente legante in quantità pari all’8-11% in peso e notevolmente ricco di frazioni fini) è del tutto simile a quelli descritti per il conglomerato bituminoso per strade. Le peculiarità consistono nel fatto che l’essiccatore deve consentire il riscaldamento dell’aggregato ad una temperatura superiore a quella necessaria per gli
altri conglomerati (200-220 C°), inoltre deve essere presente un’apposita caldaia con
mescolatore. Se il conglomerato da produrre è il gussasphalt si può fare a meno di quest’ultimo accorgimento.
In alcuni casi la ricetta del conglomerato per marciapiedi prevede l’utilizzo fra gli ingredienti di polvere asfaltica: in tal caso è possibile adottare un essiccatore a doppio tamburo coassiale dove nel tamburo interno circolano fiamma e gas di combustione, mentre la polvere asfaltica passa tra i due tamburi senza subire contatti diretti con i gas caldi e con la fiamma la cui azione produrrebbe un violento indurimento del bitume.
In altri casi è prevista l’addizione di alcuni pani di polvere asfaltica direttamente al termine della lavorazione.
Il bitume viene sempre aggiunto alla miscela mediante un sistema di spruzzatura a pressione allo scopo di assicurare un intimo rivestimento delle frazioni fini, più abbondanti rispetto all’asfalto per strade.
Il tempo di miscelazione è più lungo (alcune ore), rispetto a quello richiesto per i normali conglomerati (20-40 secondi).
ATTREZZATURE, MACCHINE, IMPIANTI
Camion a cassone ribaltabile utilizzato per il trasporto di inerti di varia granulometria dalla cava all’impianto di produzione, di asfalto fresato dal cantiere all’impianto di produzione, di conglomerato bituminoso dall’impianto di produzione al cantiere di stesa.
Trattore con cisterna utilizzato per il trasporto di filler o di bitume all’impianto di produzione.
Pala gommata per la movimentazione di inerti sul piazzale di stoccaggio e dal piazzale di stoccaggio alle tramogge dell’impianto di produzione asfalto. Possono essere coperte o scoperte. Hanno capacità di carico variabile a seconda delle dimensioni dell’impianto di produzione.
Impianto di produzione costituito da impianto di predosatura ponderale (tramogge, predosatori e nastro trasportatore), impianto di pretrattamento o essiccazione (forno a tamburo rotante), torre di mescolazione (con eventuale elevatore a tazze), silos di stoccaggio del conglomerato (con eventuale benna di traslazione).
Videoterminale nella cabina di comando per la gestione e la conduzione dell’impianto.
FATTORI DI RISCHIO
Agenti chimici e cancerogeni: è previsto l’utilizzo di sostanze o preparati attualmente non classificati come cancerogeni o pericolosi per l’uomo (bitume, conglomerato bituminoso), tuttavia i lavoratori possono venire a contatto con sostanze chimiche che si liberano proprio durante la lavorazione: gli Idrocarburi Policiclici Aromatici (IPA), alcuni dei quali sono riconosciuti come cancerogeni o pericolosi. Attualmente non è tecnicamente possibile la sostituzione di tali materie prime nel ciclo produttivo con altre meno pericolose e la lavorazione è a ciclo chiuso (ad eccezione della fase di carico del conglomerato sul camion a cassone ribaltabile destinato al cantiere di stesa). La metanalisi dei risultati di monitoraggio ambientale e della letteratura ha evidenziato livelli di IPA ben al di sotto di vari ordini di grandezza rispetto ai valori limite professionali e paragonabili a quelli riscontrabili in ambiente urbano. In particolare l’esposizione a benzo(a)pirene, inteso come tracciante degli IPA altobollenti cancerogeni, solo in limitate situazioni si è mostrato superiore al valore guida indicato
in Italia per la popolazione generale (1 ng/m3), ma ogni singolo caso è meritevole di
appropriata valutazione: valore mediano di 0,4 ng/m3, 5° percentile di 0,1 ng/m3 e 95° percentile di 5,6 ng/m3. L’esposizione ad agenti chimici può avvenire anche in occasione delle opere di manutenzione di attrezzi e mezzi giornaliera (benna, scoli, ecc.); la manutenzione ordinaria e straordinaria, che riguarda soprattutto i motori e gli
organi di lavoro soggetti ad usura, viene svolta con periodicità programmata ed in caso di necessità da tecnici specializzati di officine autorizzate.
Agenti chimici – infortuni: l’asfalto è commercializzato a temperature superiori ai
100°C: le temperature più elevate si hanno nell’asfalto modificato (fino a 200°C) e nel colato (fino a 260°C). Risulta possibile la formazione di idrogeno solforato nei siti di stoccaggio del bitume.
Agenti chimici – incendio/esplosione: il rischio di incendio non coinvolge direttamente il conglomerato bituminoso, che è da ritenersi fondamentalmente non combustibile, bensì il bitume che comunque è considerabile un combustibile a basso rischio, privo di reattività pericolosa, che può formare miscela infiammabile e bruciare con fiamma viva solamente se riscaldato a temperatura superiore al punto di infiammabilità (maggiore di 200-250°C). Né l’asfalto, né il bitume sono dotati di
proprietà esplosive. Impianti di gas combustibile sono presenti per alimentare sistemi di
riscaldamento (forno rotante, cisterna). Le aziende sono generalmente dotate di una cisterna per il gasolio dalla quale si attinge per il rifornimento dei veicoli aziendali. Nel complesso il rischio di incendio può essere considerato a livello basso o medio.
Utilizzo di macchine - infortuni: l’utilizzo di macchine a corpo rotante, macchine a piani mobili o con nastro trasportatore è comune; particolare attenzione meritano le operazioni di manutenzione durante le quali vengono utilizzati una serie di attrezzi, più o meno semplici, anche con organi in movimento o alimentati elettricamente.
Utilizzo di macchine - rumore: il rischio è stato sensibilmente ridotto con l’introduzione di macchinari di nuova concezione dotati di sistemi fonoassorbenti. I livelli equivalenti riscontrati nelle postazioni di carico inerti variano da 84 a 88 dBA e nelle postazioni di controllo produzione tra 77 e 89 dBA. L’esposizione quotidiana dei lavoratori risulta nella maggior parte dei casi compresa tra 75 e 88 dBA, ma ogni singolo caso è meritevole di appropriata valutazione.
Utilizzo di macchine - scuotimenti: il rischio si può presentare generalmente nella conduzione di pala e camion; tuttavia anche in alcuni impianti “compatti”, soprattutto per la produzione del colato, è possibile una consistente esposizione dell’operatore. I valori di accelerazione ponderata in frequenza delle vibrazioni equivalente a 8 ore di lavoro A(8) applicata alle moderne macchine oggi utilizzate sono in genere inferiori 0,5
m/s2, ma ogni singolo caso è meritevole di appropriata valutazione. In particolare i
range del vettore massimo (AWmax) del valore quadratico medio dell’accelerazione ponderata in frequenza, riscontrabili utilizzando pala gommata su sterrato e su asfalto sono rispettivamente di 0,3-1,0 m/s2 e 0,4-1,1 m/s2.
Utilizzo di macchine - videoterminale: i tempi effettivi di utilizzo del videoterminale da parte dell’addetto alla conduzione dell’impianto generalmente superano le 20 ore settimanali, perché nei moderni impianti buona parte di tempo è dedicata all’effettiva interazione uomo-macchina.
Ambiente di lavoro - infortuni: costituiscono elementi di criticità la pavimentazione, le zone di passaggio, le aree di lavoro, i movimenti di mezzi e gli impianti elettrici. Ambiente di lavoro - microclima: le lavorazioni che si svolgono nell’unità produttiva prevedono la permanenza di un operatore in ambiente confinato (cabina di controllo)
non sempre rispondente ai criteri ergonomici (dimensioni ridotte, pareti in metallo,
ampie fenestrature, spesso inserita direttamente nel contesto dei macchinari. I mezzi d’opera sono in genere dotati di impianto di climatizzazione o condizionamento. Ambiente di lavoro - polvere: polverosità nell’aria si può presentare sia durante il carico degli inerti nelle tramogge, sia per dispersioni accidentali di filler dalle tubazioni di raccordo (soprattutto durante le operazioni di riempimento dei silos). La metanalisi dei risultati di monitoraggio ambientale e della letteratura ha evidenziato livelli di polvere inalabile al di sotto di un ordine di grandezza rispetto ai valori limite professionali suggeriti da enti internazionali per polveri non altrimenti classificate:
valore mediano 0,90 mg/m3, range 0,01-1,90 mg/m3.
Ambiente di lavoro – agenti biologici: durante le operazioni che si svolgono in ambiente esterno è possibile contatto in particolare con Clostridium Tetani, le cui spore sono ubiquitariamente diffuse nel suolo, nelle acque e nel pulviscolo atmosferico. Ambiente di lavoro – radiazione solare ultravioletta: relativamente al lavoro all’aperto gli operatori sono esposti alla radiazione solare.
Ambiente di lavoro – punture di insetti: soprattutto relativamente al lavoro nel piazzale di stoccaggio gli operatori agiscono in campo aperto scarsamente urbanizzato, con possibilità di venire punti da insetti ed in particolare da imenotteri.
Movimentazione carichi con macchine: il carico delle tramogge e la movimentazione degli inerti nel piazzale vengono effettuate con utilizzo di macchine di sollevamento. Sollevamento di carichi in altezza mediante è possibile anche nella movimentazione con benna del conglomerato bituminoso diretto al silos di stoccaggio.
Organizzazione del lavoro: le lavorazioni sono svolte con cadenze operative vincolanti, monotonia e ripetitività. In genere le operazioni vengono pianificate accuratamente il giorno precedente, evitando situazioni stressanti ed impreviste.
FONTE: Profilo di Rischio nel comparto Allevamento avicolo (inailcloud.it)
Trovate l'approfondimento in formato word editabile in area condivisione gratuita riservata agli iscritti della nostra Newsletter Professional nella sezione PROFILI DI RISCHIO INAIL
ANCHE QUESTA RISORSA E' GRATUITA PER GLI ISCRITTI ALLA NOSTRA NEWSLETTER PROFESSIONAL. ISCRIVITI ANCHE TU.
Disclaimer
Il contenuto della banca dati Profili di rischio rappresenta una prima base informativa, sviluppata grazie alla collaborazione dei Servizi di prevenzione delle Asl, aperta a tutti i contributi finalizzati all’aggiornamento dei profili esistenti, all’integrazione di nuovi profili nella banca dati, al collegamento con altre sorgenti informative (Sistema nazionale di sorveglianza infortuni e malattie professionali, Banche dati su fattori di rischio, Buone pratiche, ecc.) che approfondiscono temi specifici trattati nel profilo.
ATTENZIONE: ESSENDO LA VECCHIA BANCA DATI ISPESL ASSORBITA DA INAIL MOLTI RIFERIMENTI NORMATIVI SONO ANACRONISTICI.
PERTANTO IL PRESENTE PROFILO DI RISCHIO E’ DA LEGGERSI PER AVERE INDICAZIONE DESCRITTIVA SUI RISCHI PRESENTI NEL COMPARTO MA VERIFICARE SEMPRE SE VALORI LIMITE E ALTRO SIA STATO SUPERATO DA DISPOSIZIONI NORMATIVE SUCCESSIVE.
RIMANE COMUNQUE UN UTILE STRUMENTO PER AVERE INFORMAZIONI SUI RISCHI DI COMPARTO.
Fonte:Profili di rischio Inail